Materials Management and Warehousing Consultancy
Orion Materials Management partnered with a major operator to optimise material management processes, clearing a significant backlog, preventing costly shutdowns, and delivering $15M in cost savings while improving operational efficiency and KPI metrics to best-in-class standards.
Services provided included:
Materials Management
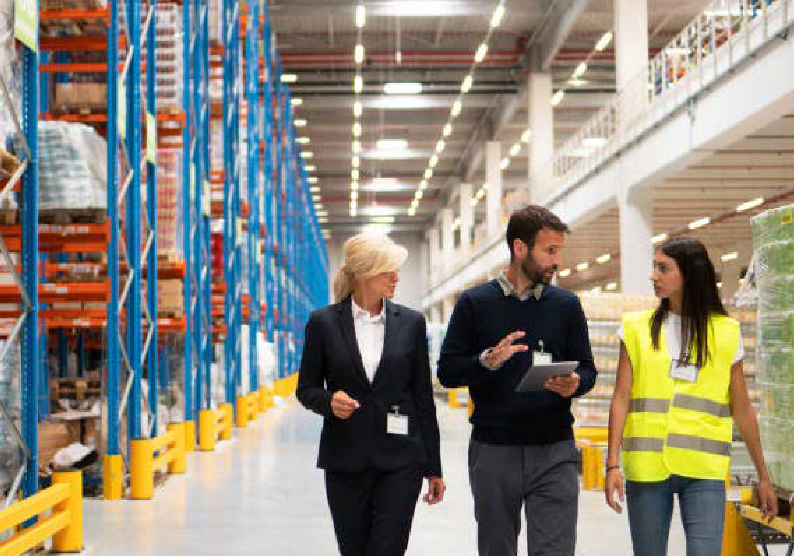
Name of Company
Major LNG OperatorSector
Oil and GasLocation
West AfricaThe Background
The Brief
Our client asked Orion Materials Management (OMM) to address the inefficiencies within their material management processes that were causing operational disruptions. Specifically, the objectives were to:
Optimise material management processes to ensure materials required for operations and maintenance were identified, controlled, reserved, ordered, and replenished efficiently.
- Resolve the system setup issues that were hindering the team’s ability to schedule and execute work orders on time, impacting plant reliability.
- Eliminate the material backlog that posed a significant risk to operations and production, contributing to unplanned shutdowns and financial losses.
- Improve accountability and provide better visibility across end-to-end processes, ensuring smoother operations.
Enhance regional KPI metrics, improving performance to best-in-class standards and aligning with industry benchmarks
The Solution
OMM’s solutions focused on optimising material management processes, improving system functionality, and enhancing operational efficiency. Key actions included:
- Process Redesign and Optimisation:
Developed robust, streamlined processes for identifying, controlling, reserving, ordering, and replenishing materials, which significantly reduced inefficiencies and improved scheduling and execution of work orders.
- Critical Spare Parts Review:
Conducted Critical Spare Parts Reviews and inventory optimisation to ensure the availability of essential materials, preventing costly unplanned shutdowns and ensuring smoother plant operations.
- System and Process Integration:
Addressed system setup issues that were previously hindering material flow and work order execution, improving system functionality for better scheduling and decision-making.
- Backlog Clearance and Automation:
Cleared 75% of the procurement backlog and set up PO automation to increase procurement efficiency and prevent future material delays.
- Materials Management Transformation Charter:
Delivered a comprehensive Materials Management Transformation Charter, covering over 25 key PSCM processes and more than 400 actions, to ensure a sustainable long-term solution.
- KPI Improvements:
Improved regional KPI metrics to achieve best-in-class performance, significantly enhancing operational efficiency and reliability.
Through these solutions, OMM addressed critical pain points, reducing operational risks, improving material flow, and driving significant cost savings and efficiency gains.
The Outcomes
The results of OMM's solutions were significant for the client, delivering significant improvements across operations and financial performance:
Cost savings of $15M through the development of robust processes for value recovery and optimisation.
- Prevention of unplanned shutdowns, saving $2.5M by conducting critical spare parts reviews and optimising inventory.
- 75% of procurement backlog cleared, with PO automation set to reach an all-time high for the region, streamlining operations.
- Materials Management Transformation Charter delivered, covering 25+ key PSCM processes and over 400 actions, ensuring long-term improvements.
- Best-in-class KPI performance achieved, significantly improving operational efficiency and setting new benchmarks in the region.
These results not only addressed the immediate operational challenges but also laid the foundation for sustainable, efficient material management moving forward